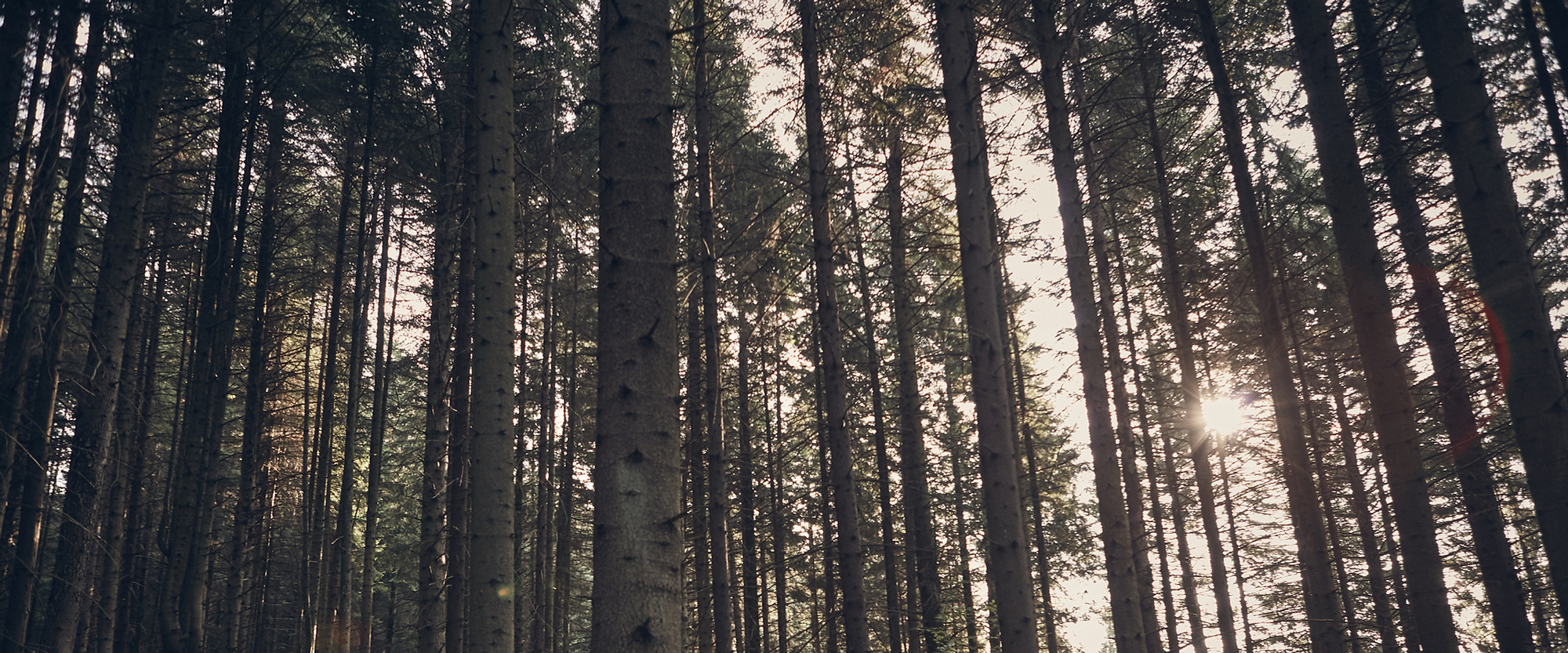
CONSTRUCTION
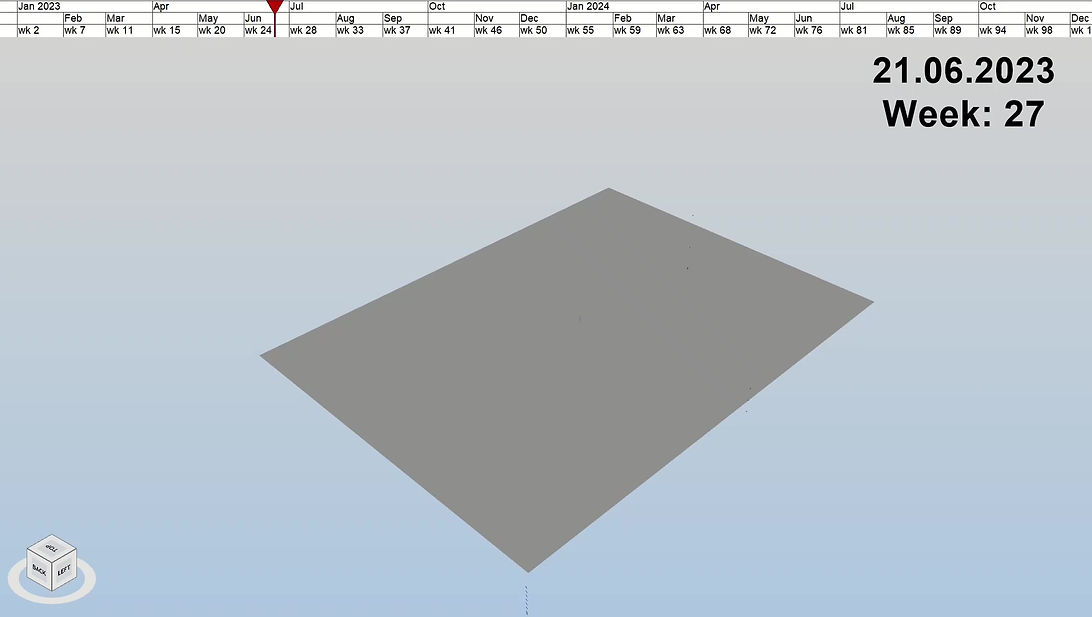


5D
MODEL
SAFETY
Here At Evergreen United, We prioritize Safety at all times. We Have been able to Maintain An EMR of 0.34 which really shows how much we care about safety. This means that we as a contractor are found to be no more or less risky than a majority of other contractors. Typically, a rating under 1.0 is considered good, or relatively safe.
RISK REGISTER

SITE
LOGISTICS
According to U.S Climate Data, Irvine has an average high temperature of 72 ºF and an average low temperature of 54 ºF. It has warm, dry summers and mild wet winters. As a result, we do not expect extreme weather to intervene with the construction process. We will plan for the occasional rainy days and be prepared to cover all material and equipment if it starts to pour. We will also ensure our crews are well hydrated and prepared for days where the tempERature reaches 90+ºF.
WEATHER
According to U.S Climate Data, Irvine has an average high temperature of 72 ºF and an average low temperature of 54 ºF. It has warm, dry summers and mild wet winters. As a result, we do not expect extreme weather to intervene with the construction process. We will plan for the occasional rainy days and be prepared to cover all material and equipment if it starts to pour. We will also ensure our crews are well hydrated and prepared for days where the tempreature reaches 90+ºF.
EXISTING LAND DEVELOPMENTS
There are very little existing land elements because the site is an empty parking lot.
The site is mostly asphalt with a couple of trees and light posts.
SITE ACCESS
There are two main roads to access the site, which are Jamboree Rd on the east side and Teller Ave on the west side. The primary road that we will use to access the site is Jamboree Rd, as trucks coming out of the highway can go directly to the site. We will be utilizing both roads to effectively move material and equipment in and out of the site.
JURISDICTIONAL CONSTRAINTS
The site is under the jurisdiction of the Irvine Business Complex (IBC) District. Their guidelines will be analyzed to determine any constraints. The following information was obtained from the Environmental Impact Report certified as part of the approval of the IBC.
Operational Hours
Construction activities occurring as part of the project shall be subject to the limitations and requirements of Section 6-8-205(a) of the Irvine Municipal Code which states that construction activities may occur between 7:00 AM and 7:00 PM Mondays through Fridays, and 9:00 AM and 6:00 PM on Saturdays. No construction activities shall be permitted outside of these hours or on Sundays and federal holidays unless a temporary waiver is granted by the Chief Building Official or his or her authorized representative.
Noise Management
Noise can be described as a sound that is loud, unpleasant, unexpected, or otherwise undesirable. In construction, it is important to monitor this disturbance to accommodate the persons near the site. In order to mitigate this disturbance, the following guidelines will be applied to the job:
-
Construction equipment, fixed or mobile, shall be equipped with properly operating and maintained noise mufflers consistent with manufacturer’s standards.
-
Construction staging areas shall be located away from off-site sensitive uses during the later phases of project development.
-
Equipment will be placed so that emitted noise is directed away from sensitive receptors nearest the project site, whenever feasible.
-
Construction of sound walls that have been incorporated into the project design prior to construction of the building foundation; or installation of temporary sound blankets (fences typically composed of poly-vinyl-chloride-coated outer shells with adsorbent inner insulation) placed along the boundary of the project site during construction activities.
Dust Control
Applicants for new developments in the Irvine Business Complex shall require that the construction contractor prepare a dust control plan and implement measures under the South Coast Air Quality Management District Rule 403. The following measures will be implemented to control dust:
-
During all grading activities, the ground cover on the construction site will be reestablished through seeding and watering.
-
During all construction activities, the streets will be swept with Rule 1186 compliant PM10-efficient vacuum units on a daily basis if silt is carried over to adjacent public thoroughfares or occurs as a result of hauling.
-
Trucks carrying material can produce dust. A minimum 24-inch freeboard on trucks hauling dirt, sand, soil, or other loose materials and tarp materials with a fabric cover will be used to mitigate this.
-
Ground surfaces and disturbed areas will be exposed a minimum of every three hours on the construction site and a minimum of three times per day.
-
On-site vehicle on unpaved roads will have a speed limit to no more than 15 miles per hour.
Overhead Restrictions
There are no overhead restrictions on site. The only possible restriction is the powerlines that run through Jamboree Rd.
TRAFFIC FLOW
Entrance and Exits
There will be one entrance and one exit on Jamboree Rd, and one entrance and one exit in Teller Ave.
One-way Routing or Two-Way Traffic Flows
Entering the site will be through Jamboree Rd. Once the trucks enter the site, they will exit through Jamboree Rd as well. The exit will be one-way and the trucks will exit right after leaving the site. Teller Ave is two way, and allows trucks to make left or right turns when leaving the site.
Pedestrian Crossing Areas
There is a pedestrian curb next to Jamboree Rd. There are no pedestrian cross areas on Teller Ave.
Parking Areas For Crew Parking
No parking is allowed on Teller Avenue due to the fine lane, Teller ave is a red zone therefore no stationary vehicles on Teller Ave. As a result, parking will be in the adjacent business parking lot of the site.
AREAS FOR MATERIAL STORAGE
Critical Considerations include:
-
Physical size required to fit materials
-
Weather protection required
-
Accessibility of people and/or large equipment for distribution to the site
-
Security to deter theft
BUILDING ACCESS
The traffic flow, materials storage, and temporary facilities can’t conflict with the areas of work. As a result, we will need to keep in mind of the following factors:
-
Proximity to crew parking areas to reduce travel path
-
Access roads for equipment, such as the crane that will be utilized
-
Ground preparation required for temporary access
SITE SECURITY
One component of the logistics plan is to plan for site security to ensure equipment and materials are safe. The following methods will be implemented to ensure the site is safe, and deter any theft:
-
Security cameras with motion sensors
-
Site fencing
-
Use of Conex boxes for secure tool storage
-
Staging equipment to block gate access
-
Removing keys and batteries out of equipment
-
Lifting generators and other expensive equipment with cranes
-
Hiring site security to regularly patrol the area
CREW RELIEF AREAS AND SITE OFFICES
It is important for construction crews to have relief areas to maintain labor productivity and ensure workers have areas where they can rest. The following items and areas will be provided:
-
Site office, with ample meeting space
-
Break areas with clean water and possibly small appliances for meal prep
-
Hand washing stations
-
Portable restrooms
-
Shade locations
-
Emergency meeting areas
SCHEDULE
In order to effectively manage a complex project, a detailed schedule consisting of over six hundred activities was meticulously crafted utilizing Primavera P6, a project management software that enables precise planning and tracking of project progress. Regular updates were performed to ensure alignment with the architectural and structural design, as well as to monitor project advancement.
​
However, despite careful planning and diligent execution, unforeseen circumstances can sometimes arise, resulting in delays that threaten to disrupt the project schedule. In such cases, effective solutions must be implemented to recover lost time and prevent any undue extensions to the final completion date.
​
To address such contingencies, our project team implemented remedial measures to effectively make up for lost time and maintain the project's schedule. This proactive approach enabled us to meet all project milestones and deliver the final project on time, within budget and to the satisfaction of all stakeholders involved.
PROJECT MILESTONES

CONSTRUCTION
SEQUENCE
Our design consists of three mass buildings in a tight area adjacent to business buildings and offices. As a result, we must ensure our construction sequence takes into account these variables and does not create any conflicts with logistics. In order to avoid this, we subdivided our buildings into segments to phase out the process and ensure the workers remain on site until their area of work is complete.
PROJECT MILESTONES
We subdivided our buildings into segments to phase out the process to ensure the workers remain on site until their area of work is complete.
​
An illustration of this subdivision can be seen in the diagram on the left. The classroom is subdivided into five segments (C1,C2,C3,C4, and C5), the lab is subdivided into two segments (L1,L2) and the gymnasium is subdivided into two segments (G1 and G2).
​
The segments will be constructed simultaneously based on the color they have. For example, C2 and L1 segments will begin foundation at the same time.
The classroom will lead construction as it will be the first to start and the last to finish.

By phasing the construction sequence in this matter, workers do not leave the site until their scope of the project is completed. The same workers are utilized throughout the process ensuring consistent work. If we decided to work on one building at a time, the workers would have to leave the site with all their equipment and tools and then come back later to work on another building. This could cause issues with logistics and could potentially delay the project.
To demonstrate how this process occur, we utilized Synchro which is a software program which allows us to construct, plan, and visualize the project by using both Revit 3D models and our imported P6 Schedule. The video starts off in week 24 after the preconstruction activities have occurred.

COST
ESTIMATE
To develop our cost, we accurately performed a quantity takeoffs from the drawing plans produced by our Design Team. Our cost was broken down into materials, labor, equipment, and any other expenses for the project. It was further broken down into their separate Divisions defined by the Construction Specifications Institute (CSI). Timber and CLT panels took 23% of the overall cost because all our three buildings mainly composed of wood. We have also taken into consideration all the unforeseen circumstances and potential contingencies during the construction phase. All costs were obtained through RSMeans and research.

S-CURVE
A graph that tracks the project's progress and more effectively allocate the resources for a more efficient progress. It is also used to determine if the project is on schedule and on budget. With the use of Primavera P6, we were able to analyze and produce our S-Curve to easily visualize the efficiency of our schedule and adjust accordingly for a higher productivity while still stay within the budget.
